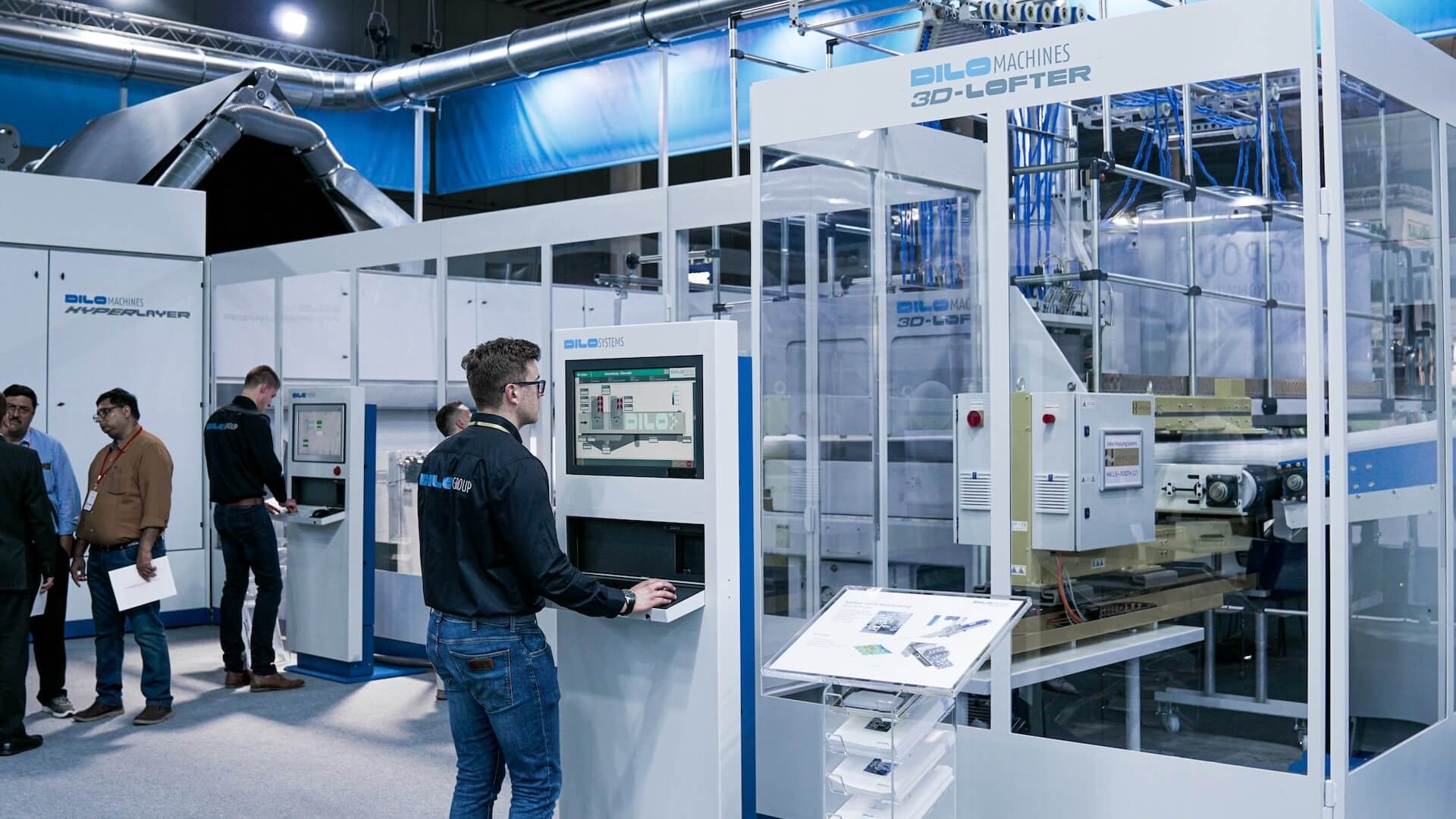
Popular Industrial IoT Use Cases in Smart Factories
Replacing human activity with connected devices in many manufacturing processes has revolutionized the image of manufacturing.
Remote monitoring: IoT devices can monitor industrial processes without the need for human presence. This solution can help companies better manage production activities, save operational costs and ensure quality, especially when operating multiple plants in different locations.
Predictive maintenance and optimization of machinery and equipment performance: by collecting data from sensors (related to temperature, revolutions, pressure, voltage, etc.) and combining it with data related to operation history, maintenance history, and operation schedules, the ...... system predicts failures and arranges for service teams to carry out maintenance according to operation schedules, thus minimizing the risk of equipment downtime and optimize equipment uptime.
Digital Twins: Digital copies of equipment and plants, including design, operations, and maintenance data, enable companies to simulate multiple processes, conduct tests, identify problems and provide remedies without risking or damaging actual assets, as well as support production schedules and optimize equipment and operational process uptime.
Ensure occupational safety: In hazardous work environments, workers can be equipped with smart wearables connected to a control center to measure and detect problems, such as monitoring personal health, determining safe distances from machines, and detecting gas leaks ...... can help factories detect problems faster and respond in a timely manner.
Barriers to Industrial IoT Technology Adoption
Although Industrial IoT is changing the future of the industry, it is difficult for organizations to implement this technology. Here are the common challenges organizations face during implementation:
Investment Cost: Industrial IoT solutions are relatively expensive to implement. Although one of the main benefits of Industrial IoT is increased productivity and reduced costs, companies are unsure if the solution will deliver the expected return on investment.
Connectivity: one of the main requirements for applying Industrial IoT is the collection of reliable data from devices. However, there are many reasons why data cannot be collected from older devices and devices that do not support data collection or follow different specialized protocols.
Cybersecurity: industrial IoT devices also bring more security vulnerabilities to organizations. When attacked, in addition to losing important data, these devices can be misused and shut down, which in turn can affect a business's reputation and finances.
Employee skills: Training or finding new employees who can develop, deploy and operate modern Industrial IoT solutions is a huge challenge for many organizations.
Implementing an Industrial IoT Strategy: Transforming Factories into Smart Factories Step by Step
Status quo assessment: reviewing the status of equipment systems, production lines, industrial processes, and the various issues facing the factory. In China, in many industries, equipment may have a low level of automation, have limited access to data or do not follow mainstream industry protocols, which is a common reason why companies have difficulty adopting Industrial IoT technology.
Identify goals: After assessing the current state of the factory, companies need to identify the problems that industrial IoT technology can help solve and prioritize areas or processes that will have a significant impact on the factory's production activities. Typically, manufacturing companies need to prioritize basic issues such as data collection and real-time monitoring of plant operations. With access to data, companies can address other issues such as optimizing operations, predictive maintenance, and more...
Finding partners and solutions: Depending on the issues raised, organizations need to find the right partners and technology solutions to have the approach and roadmap to solve a particular problem. In addition to the technical issues, an overall assessment of the cost and effectiveness of the solution is required.
Testing and implementation: For solutions that have a significant impact on plant manufacturing operations, testing the solution on a small scale is critical to assess technical feasibility, compliance with current processes and economics. After successful testing, organizations can deploy the solution on a large scale, applying it to many different departments.
Industrial IoT technology is an important factor in the digital transformation process of manufacturing companies. However, many industrial companies lack the relevant talent to implement these steps in a systematic and organized manner. Therefore, companies need to look for professional and experienced digital transformation consulting partners to develop strategies and roadmaps to implement appropriate projects, minimize risks, and ensure successful digital transformation.